In our daily lives, most of us have extended Maslov’s hierarchy of physiological and safety needs to include power and connectivity. Those needs now extend into industry. A hospital cannot run without power for its diagnostic machines or connectivity to retrieve patient records. Nor can a factory operate without power for the robots and connectivity to control them.
Nowadays, connectivity is ubiqitous, and like ubitiquitous energy 150 years ago, it is causing a revolution. The oximeter on a patient’s finger and the respirator on her chest can easily fall off when the patient moves, causing frequent alarms, many (even most) of which are not urgent. But were those devices were connected and both generated an alarm simultaneously that would indicate an issue with the patient that needed to be addressed. Stat.
Similarly, robots in a factory can be monitored to implement predictive maintenance. Were we to ‘connect’ them, by comparing their operation over time we would then be able to understand why this robot is performing better than that one. Or compare the data from separate factories by analyzing all their data in a data center (“in the cloud”) to gain insights.
This is the industrial internet, or the industrial internet of things (IoT). It is wide, spanning multiple industries (using machine learning or data analytics in healthcare and manufacturing, for instance) and deep (from machine control to big data), so wide and deep that one company could never dominate it. Rather, firms must collaborate to gain the considerable benefits, estimated by Evans and Annunziata[1] to be US$32T, or 46% of global GDP.
This was the impetus for the Industrial Internet Consortium (IIC), which was founded in 2014. Over these last seven years, we have published multiple frameworks that lay the foundations of the industrial internet. Now it is time to build on these foundations and focus on deployments.
Large industrial industrial companies are cautious by nature. During the time it has taken to write this, my phone may have updated itself twice. You don’t do that in a hospital or factory. Risk must be considered. Is a 5% productivity improvement worth the 0.5% risk that the factory could be down for months? Safety and compliance checks must be made and these cost time and money.
So we must make haste slowly. Talking of hot technologies will not cause them to be deployed, rather the opposite as technology end users take fright. Rather, we must identify pain points. Pain could affect, for example, company operations, productivity or economics, human health and safety, customer satisfaction and product quality. If there is no pain, there is no motivation.
Once we know we have a problem to solve, and the motivation to address it, we can apply digital transformation enablers. These are the set of tools and technologies that make up the technology stack that is the industrial internet. Digital transformation enablers enable digital transformation (hence the name!) and transformational business outcomes.
Digital transformation is the notion that digitization and digitalization can transform a business, reducing costs, increasing efficiency, sustainability, and other good things.
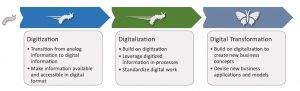
Digital transformation enablers can be applied across industries and applications. For example, a digital transformation enabler such as machine learning, when coupled with technical frameworks, standards, policies and strategies that dictate its applicability, enable transformational business outcomes across multiple industries and applications.
As another example, over-the-air updates are of special interest in automotive so that software can be updated when needed. Tesla’s update during Hurricane Irma is the classic example. (Other electric vehicles are available.) No time, in this context, to take the car to the shop!
But over-the-air updates are also useful in healthcare. Consider a farmer in South Asia with a heart condition. A trip to the doctor can be arduous and expensive, in terms of both time and money. Let’s say the doctor provides a device to measure the farmer’s heart rhythms and remit the results to the doctor. If new software becomes available—or, more urgently, there is an error in the software—it would be far preferable to upload an update over-the-air, either directly or via a mobile phone than to ask the farmer to make the long trek into town. Similarly, sending a technician to a remote oil well can be prohibitively expensive and, in some cases, dangerous.
So the issue here is how to identify the intersection between digital transformation enablers (the technologies that make up the industrial internet) that span verticals and specific pain points suffered by technology end users and their companies.
The need to span verticals and to focus on deployment has triggered a rebranding of the IIC. We are seven years old, which is 49 in dog-years and 343 in technology-years. “Industrial” to many (especially in Asia) connotes manufacturing, but IoT can be applied in health care, transportation, smart cities and so on. We do not want to dilute its impact. At the same time, we want continue to focus on the technologies that are the core of what will be deployed. Hence the rebranding to Industry IoT Consortium.
There is now an industrial internet market (job done!), so we must now look to more deployments. To increase deployments, we must identify the intersections between digital transformation enablers and the pain felt by technology end users. Then we must reduce both their actual and perceived risk. That is IIC’s mission: “To deliver transformative business value to industry, organizations and society by accelerating adoption of a trustworthy internet of things.” Let’s realize as much as we can of that that $32T!
[1] Pushing the Boundaries of Minds and Machines, Peter C. Evans and Marco Annunziata, November 26, 2012